Case study: A Basket Case by Noa Zaidman
Follow along Noa Zaidman’s design journey to accomplish a unique basket piece made with seamless technology.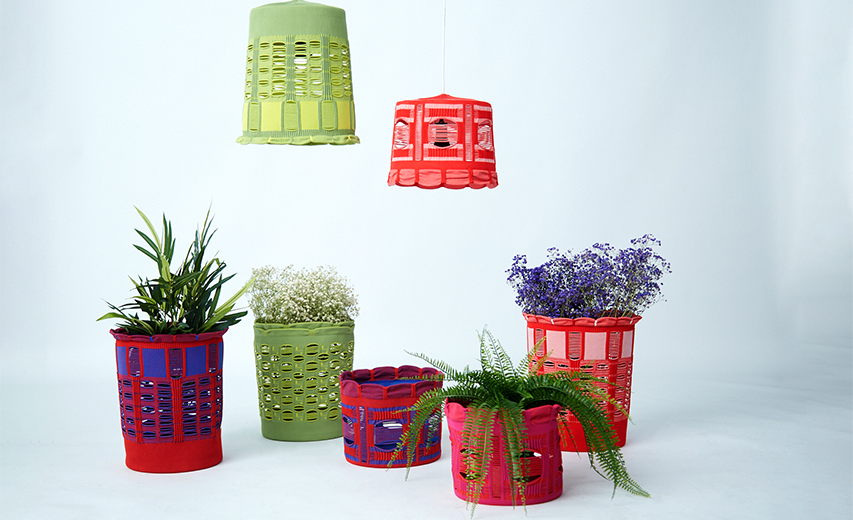
Introduction:
Noa Zaidman is a textile and fashion designer from the Netherlands, graduated from the Bezalel Academy of Art and Design. Noa participated in the last Santoni Pioneer Program with her collection “A Basket Case,” which focuses on digitizing the craft of hand-woven baskets using circular seamless technology, in order to create unique home textiles and products.
Design Concept
Noa's collection, "A Basket Case," draws inspiration from the ancient art of hand-weaving baskets—a craft that has spanned millennia across diverse cultures and communities. This time-honored practice demands patience, skill, and meticulous attention to detail, resulting in exquisite and functional pieces of art. Noa's objective with this collection was to replicate the aesthetics and tactile qualities of a woven basket using seamless technology, creating a product that could serve both as a basket and a lampshade.
To bring her vision to life, Noa initiated the creative process by sketching rough ideas, facilitating clear communication with the technicians. Subsequently, she embarked on a journey of exploration, harnessing the capabilities of the machine. This involved experimenting with various yarns, stitches, and combinations to realize her artistic vision.
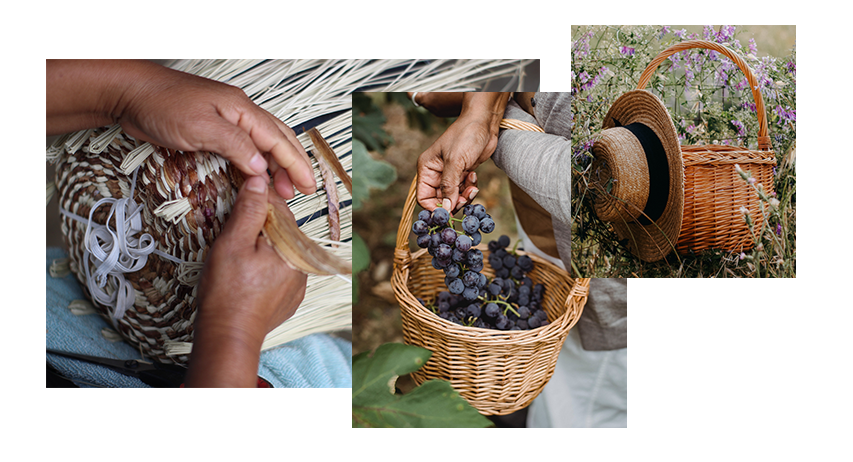
PROTOTYPE NO.1
Technical information:
Machine: TOP2 FAST
Gauge: 22
Yarns: recycled polyester, cover elastane, melting yarn.
For this product Noa used melting yarn due to its ability to shrink and stiffen up when steamed. One of the key characteristics she wanted to achieve in her product was the stiffness, in order to allow the baskets and lampshades to maintain a sturdy structure.
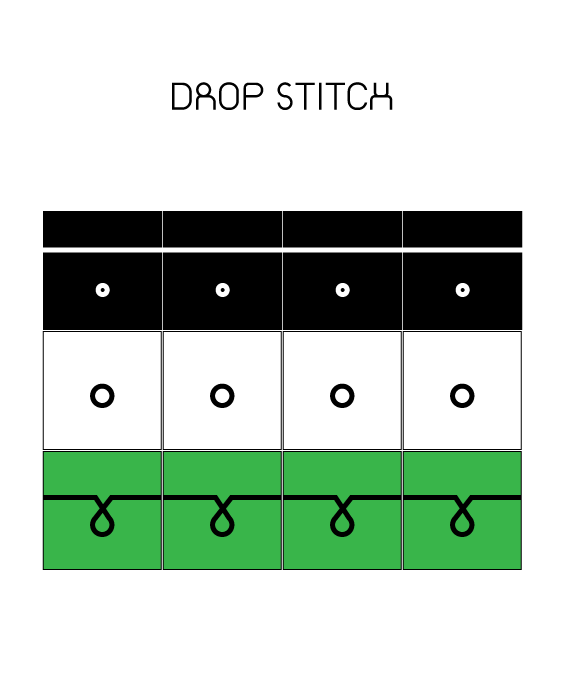
In this project TOP2 FAST machine was selected because of two reasons:
-
Utilizing Melting Yarns: Melting yarns, given their thickness, require the use of a low-gauge knitting machine for proper knitting. Consequently, the largest available gauge was 22.
-
Incorporating Drop Stitches: To attain the desired weaving effect, a dropped stitch structure was essential. This could only be achieved using a single jersey (SJ) machine, rather than a double jersey machine.
The Process
To imitate the look-and-feel of a woven basket, Noa used dropped stitches and slowly reached the point where the knitted areas between the holes (dropped stitches) looked like ropes, discovering that she could create “ropes” with different patterns by changing the knitted areas that created them. By playing with the “ropes”, the holes, and the fully knitted elements she was able to achieve a basket weaving effect in her product.
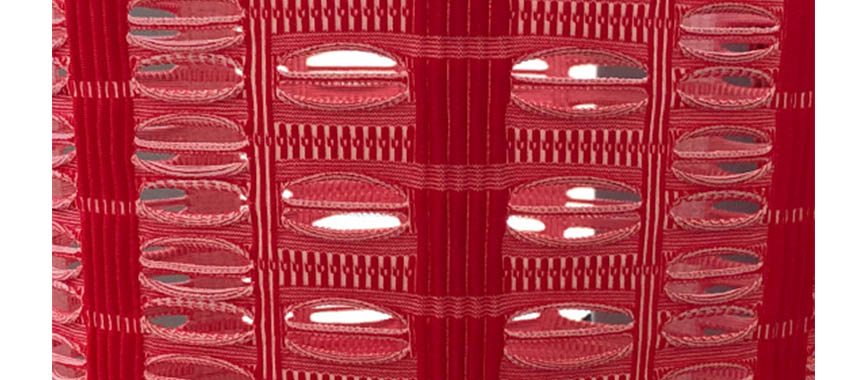
Outcome:
During the initial prototype phase, several challenges emerged. Firstly, the structural integrity of the basket proved suboptimal, as it struggled to maintain its shape effectively. Secondly, the repetitive pattern posed an issue. To enhance the basket's stability, it became necessary to reduce the number of dropped stitches in the base, thereby reinforcing its structural integrity.
The third challenge stemmed from the use of melting yarn at the basket's edge. Given that the basket's closure relied on a dial jack mechanism, the thickness of the melting yarn exceeded the machine's handling capacity.
The final challenge encountered in this initial iteration pertained to the basket's round shape. Achieving a perfectly round shape necessitated steaming the basket with the aid of a frame and allowing it to cool for several hours.
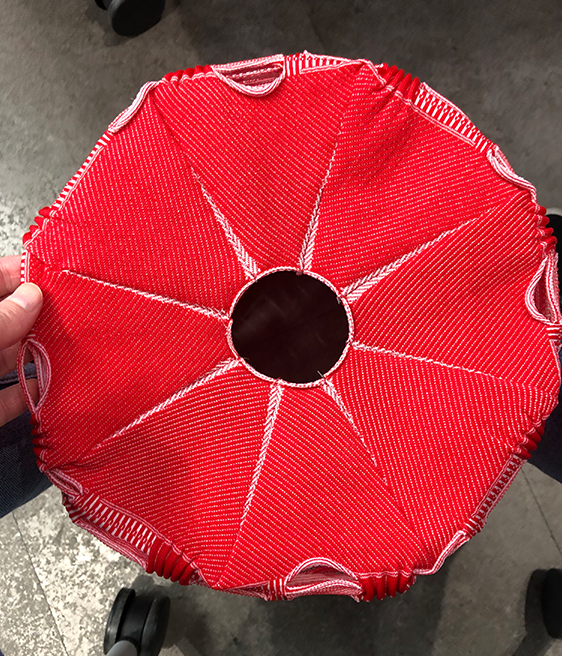
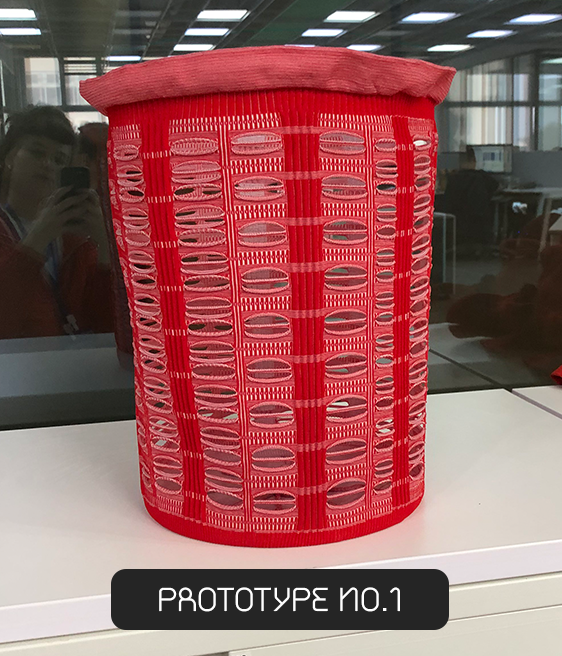
In the second iteration of this product, Noa invested time in modifying both the bottom (dropped stitch area) and the top section of the basket. During this phase, Noa made a pivotal decision to create a product with dual functionality: serving as both a basket and a lampshade. For both applications, the design of the top area played a critical role. It needed to strike a balance—not too large to prevent items from falling out when used as a basket, yet not too small to accommodate an electrical cord when used as a lampshade.
To enhance the item's structural integrity, a mock-ribbed section was introduced to reinforce the basket's bottom.
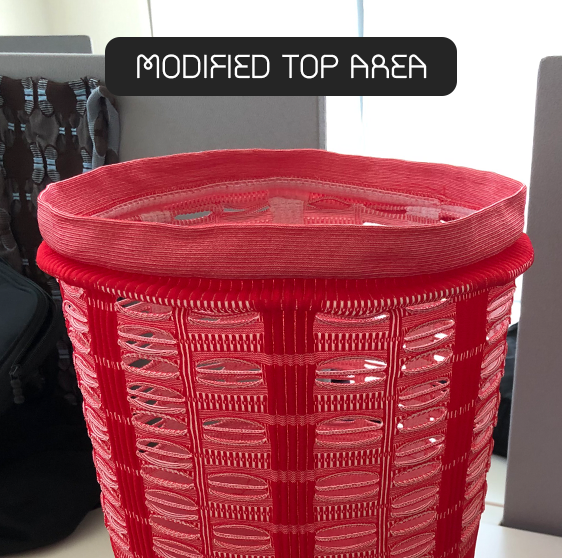
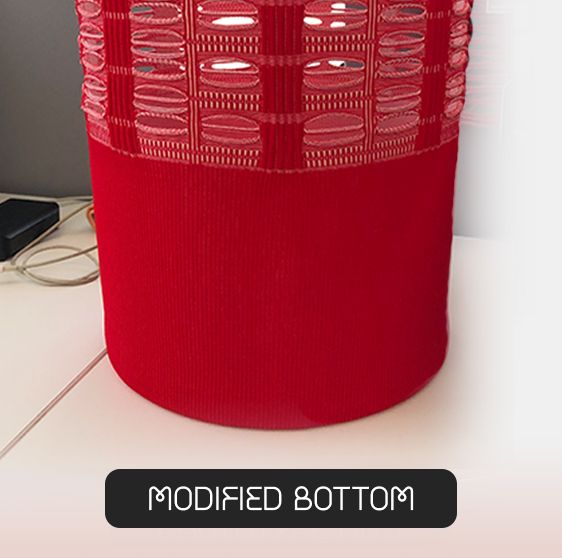
You might be interested in:
Digital Economy, Shaping the future of Manufacturing
An in-depth conversation between key industry players in seamless manufacturing about the digital economy
Read moreTrend Report: Biomimetics of Structure
The ultra-lightweight stitches that are being inspired by cellular structures.
Read moreTrend Report: 3D Therapeutic Patterns
How the therapeutic effects of paper folding influence our 3D textiles
Read morePROTOTYPE NO.2
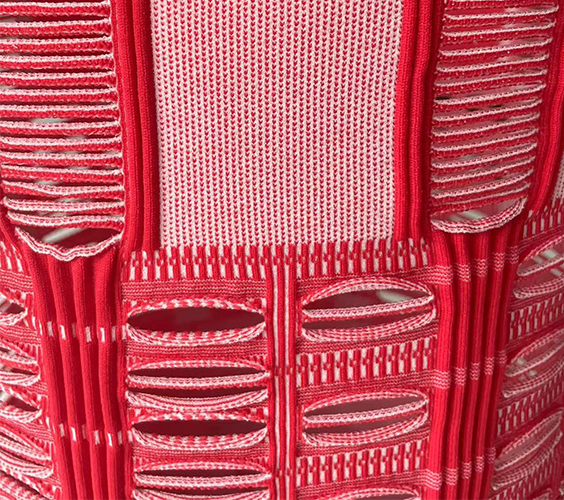
Outcome:
The prototype came out with better structural strength, but the mock-rib area ended up being too wide. The second pain point for this iteration was the edge of the basket: it was still not achieving the desired look and feel.
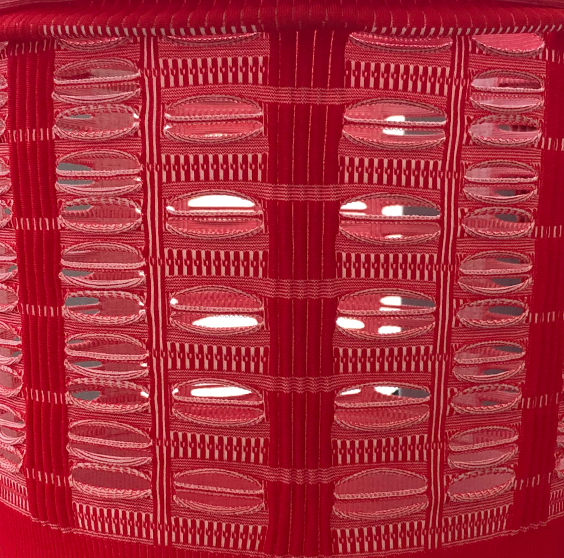
FINAL PRODUCT
In the ultimate iteration of the item, several adjustments were implemented. Firstly, the mock-rib section in the basket's bottom was made smaller to achieve a more aesthetically pleasing balance between the mock-rib and dropped stitch structures.
Furthermore, for the basket's edge, a ruffled design was adopted. This was accomplished by combining two structures, ensuring the item's structural integrity while adding a decorative touch.
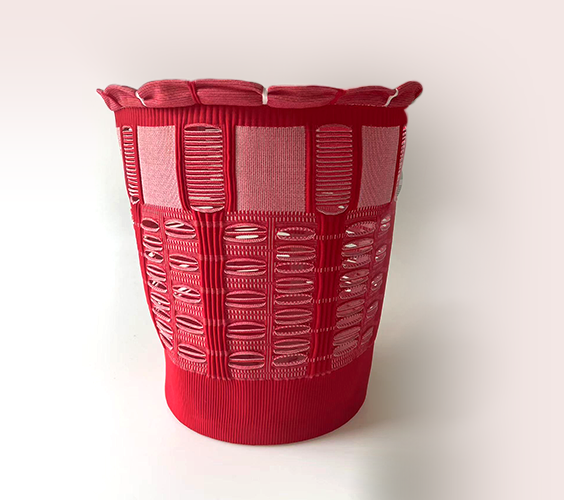
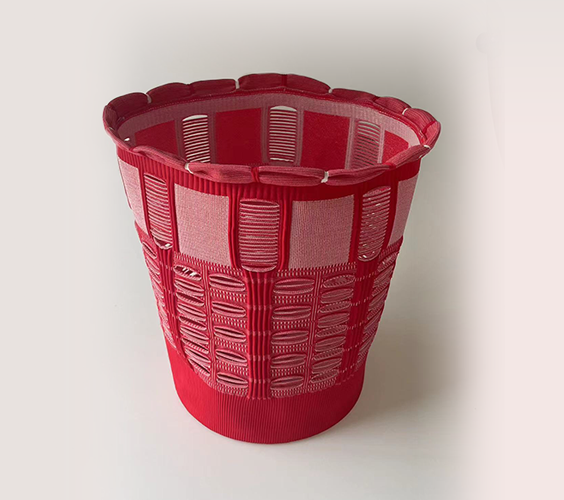
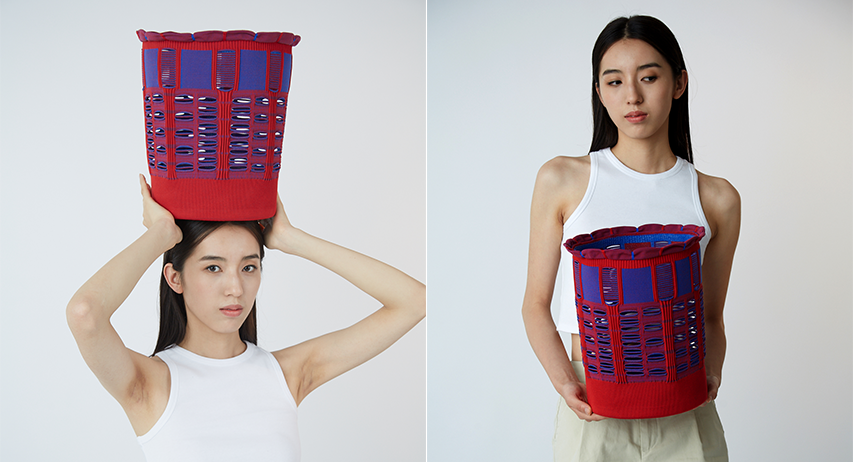
Lessons Learned:
Some of the most important lessons gained by Noa Zaidman while creating her collection at SPP were, not only learning about seamless knitting technology, but also reimagining the process of crafting objects in light of the technology's capabilities and constraints. Additionally, the program introduced her to a diverse realm of yarns and their potential applications.
Another big lesson learned during her process was how to communicate with the technician: preparing files and knowing what information he needs in order to work. Having a common language and understanding each other properly to have a successful outcome.
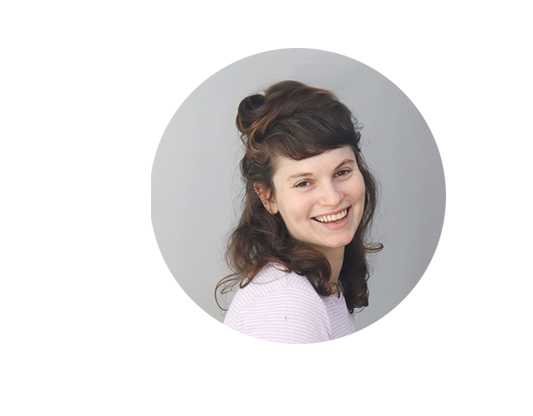
About the designer
Noa Zaidman is an Israeli product and textile designer currently located in the Netherlands. She focuses on exploring the intersection between craft and technology within textiles.
Her projects often involve pushing the boundaries of what's possible with certain materials or techniques. Colour is an essential element in her design aesthetics, and using it to create playful and eye-catching pieces. She also likes to incorporate humor into her work, as she believes design should be fun and engaging.
Website: https://www.noazaidman.com/