Case Study: “Fishbone” corset by Lynn Liu
A supportive and stylish corset construction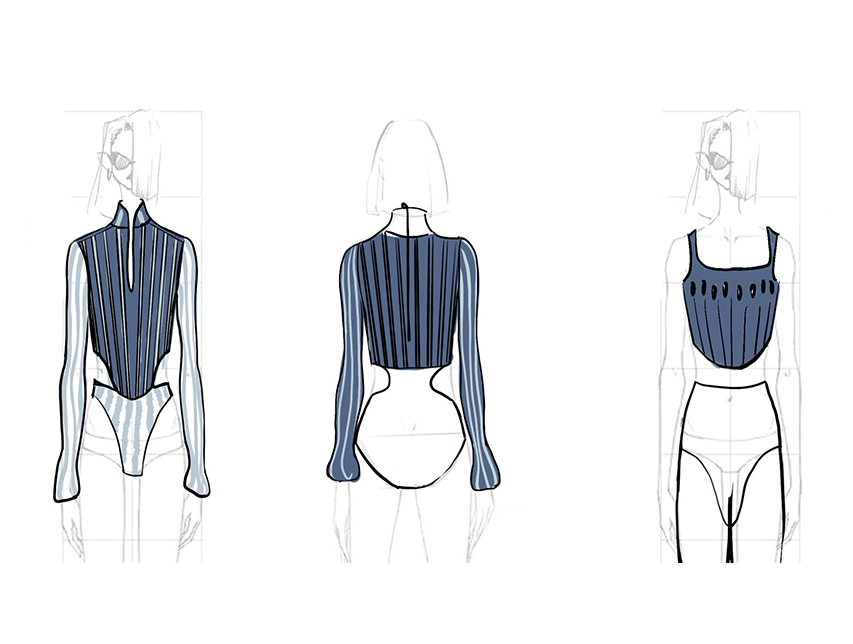
Introduction
In this case study we will explore Lynn Liu’s collection “Fishbone”. This collection was created during her participation at the Santoni Pioneer program, and it was inspired by the fishbone structure in corsetry.
This case study not only covers Lynn’s conceptual work to start her collection, but also the technical difficulties and solution she was able to find along her journey and exploration with seamless and circular technologies.
Follow along Lynn’s research and development process and learn with this innovative garment.
Background
Traditional corsetry refers to the art and craft of creating corsets, which are tightly fitted garments worn to shape and support the torso, typically by reducing the waist and emphasizing an hourglass figure. Historically, corsets have been worn by both men and women, but they are most commonly associated with women's fashion, particularly from the 16th to the early 20th centuries.
Key Characteristics of Traditional Corsetry:
Structure and Boning: Traditional corsets are characterized by their rigid structure, achieved through the use of boning (originally made from materials like whalebone, steel, or reed). These bones are inserted into channels sewn into the fabric, providing the necessary support and shape.
Fabrics: Traditional corsets are made from sturdy, non-stretch fabrics such as cotton, silk, satin, or brocade. The outer fabric is often decorative, while the inner layers are designed for strength and comfort.
Waist Reduction: One of the primary functions of a traditional corset is to reduce the waist circumference, creating an exaggerated hourglass figure, which depends on the design and the wearer's preference.
Health and Comfort: Corsets have also been used for medical applications, using the bases of traditional corsetry, new developments have been crated to support people’s torsos, enhance the posture and provide relief.
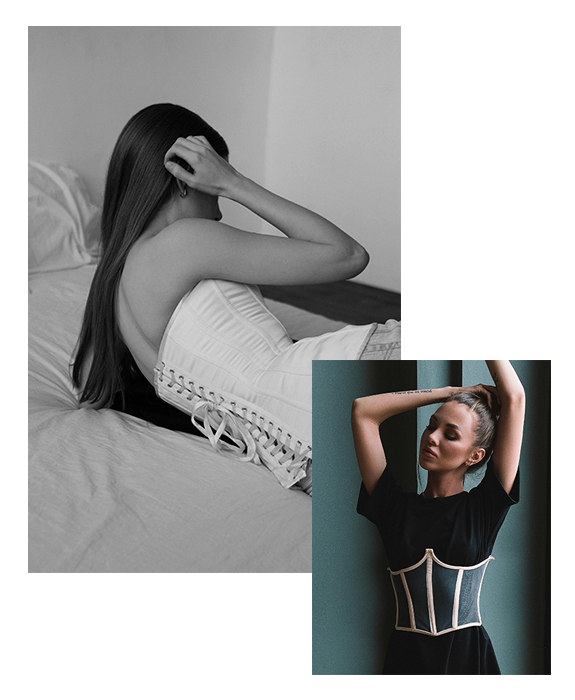
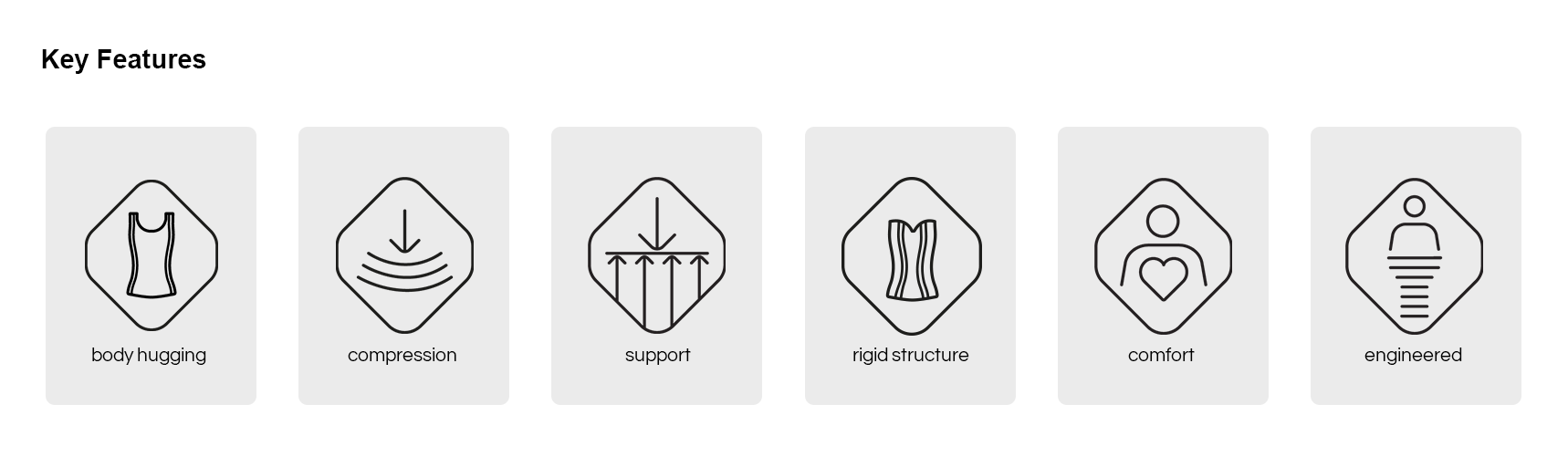
PROTOTYPE NO.1
Technical Information
Product: Corset top
Machine: TOP2 FAST
Diameter: 16”
Gauge: E28
Yarns: A1012 Volcanic Mud polyester Yarn, A1407 melting nylon
Process
During the creation of her first prototype, Lynn decided to make a test in a TOP2 FAST machine of 16” diameter, which would give her an ideal circumference to create a wearable garment. Her test features a “chain-like” structure that runs vertically in the sample, contrasting with the rest of the surface which is smooth. In order to achieve the desired effect, Lynn selected a melting nylon yarn that could be able to stiffen enough and simulate the boning structure of a corset.
This first sample proved to be too hard and too small in size to be worn, and would not be suitable to be as flexible and soft to the touch for the user, resulting in a rigid and constrictive garment. Even though this first test achieved the desired look, it was not satisfying enough to build a wearable garment.
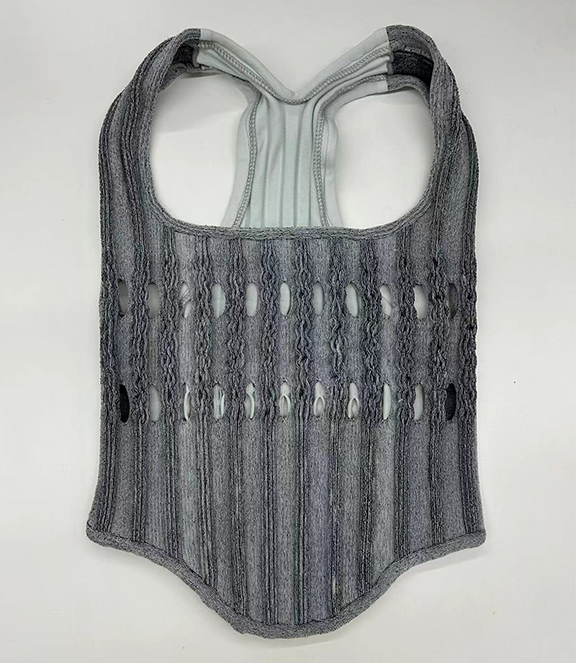
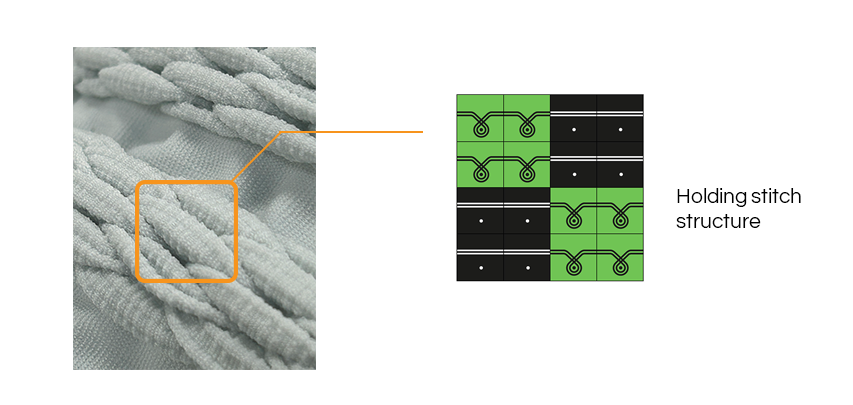
Outcome
This first sample proved to be too hard and too small in size to be worn, and would not be suitable to be as flexible and soft to the touch for the user, resulting in a rigid and constrictive garment.
Even though this first test achieved the desired look, it was not satisfying enough to build a wearable garment.
PROTOTYPE NO.2
Process
For her second prototype, Lynn decided to follow her technician’s advice and move to a wider diameter machine, in this case they used the TOP2 FAST with an 18” diameter, which provides the same capabilities as the 16” used before, with the advantage of giving a wider circumference while knitting a garment.
This change in machine diameter would correct the issue of having a small garment that would be too tight and uncomfortable for the wearer.
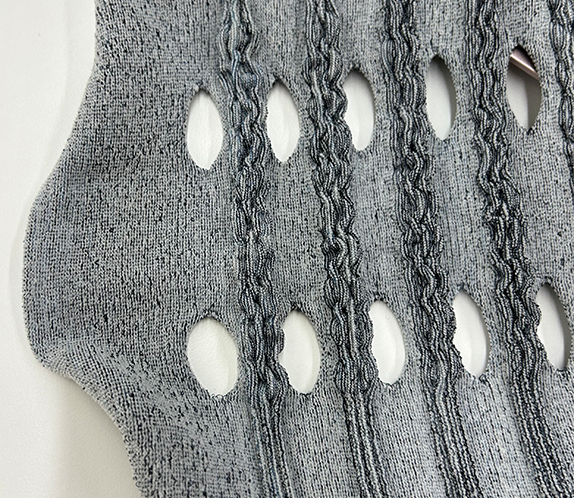
Outcome
Another of the modifications to this prototype are the yarns, in this case Lynn changed to a nylon yarn which provided a softer touch, elasticity and overall performance.
The last of the modifications was the play of the structures and tension, which allowed her to achiev her desired effect: a 3D vertical stripe, with a chain-like detail at the center of the garment.

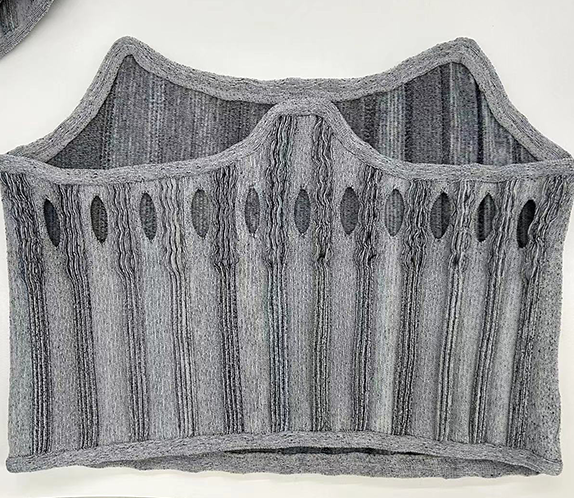
KEY LEARNINGS:
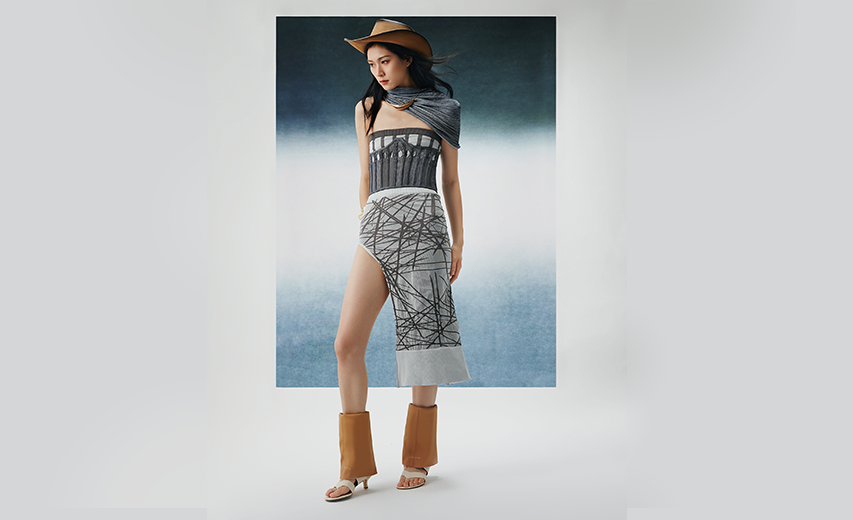
The key learnings for Lynn were the right choice of structures and yarns, which helped her to achieve the desired outcome, as well as the use of melting yarn which replaced the use of “bones” used in traditional corsetry construction.
The result is an exceptional garment that is not commonly manufactured with seamless and circular technology, inspired in a traditional product with a modern twist, and created with the latest seamless technology.

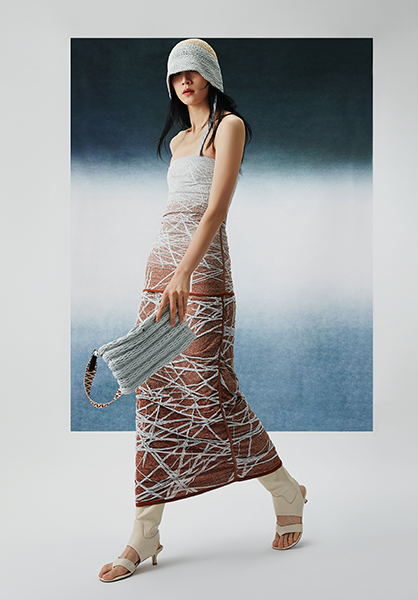
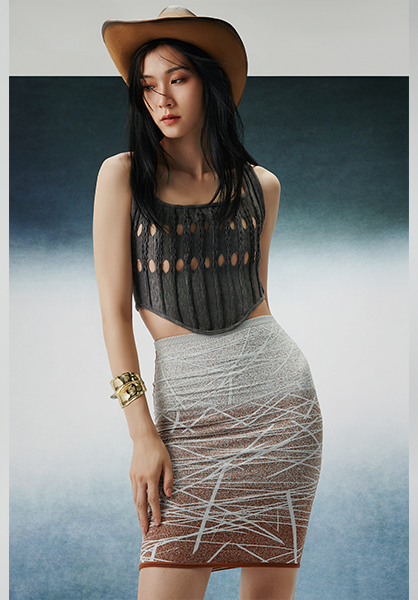
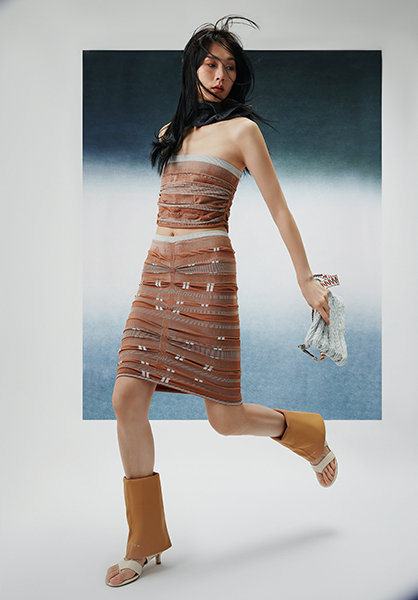
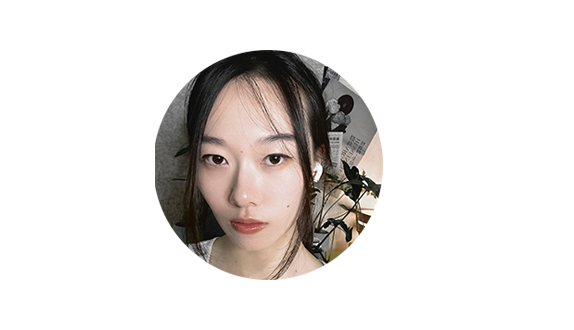
About the Designer:
Lynn Liu is a Chinese Fashion designer, major in women's ready-to-wear design at ESMOD Paris. She is passionate about art and creativity.
You might be interested in:
Case Study: Pass Unbounded
Explore designer Shearer Guo work process thru her collection “Pass Unbounded”
Read moreTrend Report: Industrial Color
How the newest colors are being used on interiors and exteriors
Read moreCapture your fabrics using Vizoo Scanner
An easy workflow to get your best results with Vizoo Scanner
Read more